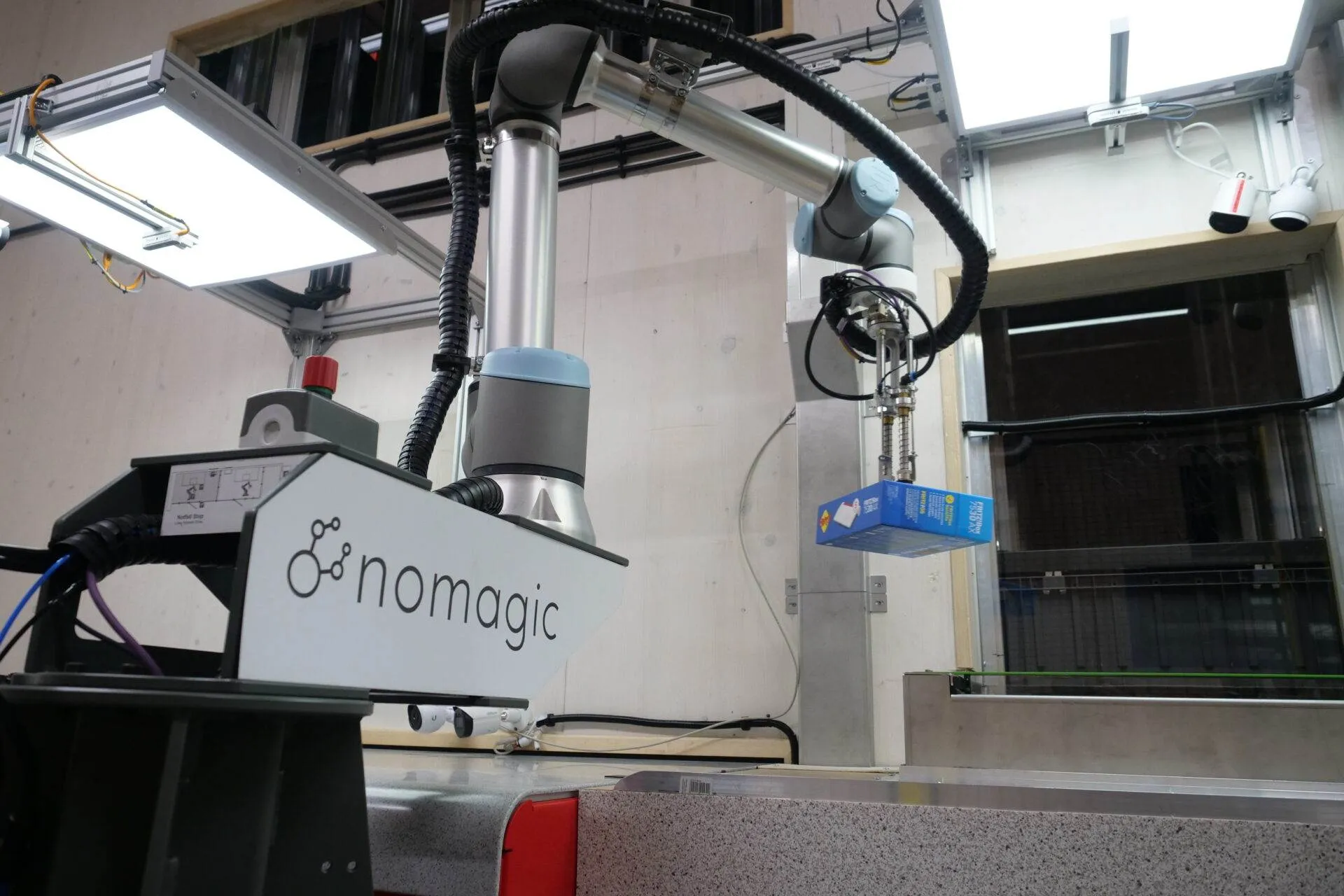
Industrial grippers are designed to automate tasks traditionally performed by human hands, which are highly advanced tools shaped by millions of years of evolution. A human hand has five fingers, twenty-seven degrees of freedom, and provides both force and touch feedback. It is adaptable and incredibly precise. However, current technology does not yet allow for the creation of such sophisticated grippers at a reasonable cost while maintaining high reliability.
To bridge this gap, engineers seek simplifications that preserve core functionalities while ensuring these innovations do not bankrupt the company. These functionalities can vary depending on the application. In the case of bin picking, key capabilities include:
Different types of grippers achieve these functionalities in distinct ways. For example, a suction cup gripper may rely on pressure feedback to determine whether it is holding an item, while a finger-based gripper is more likely to use position feedback. Although the implementation varies, the underlying signal remains the same.
Regardless of the grasping technology or manufacturing process, these four fundamental principles can guide the development of effective grippers for bin picking applications.
Attempting to design a single gripper, capable of handling everything a human hand can, will likely result in a costly, intricate system with multiple points of failure. If an application requires handling a wide variety of items, it is more practical to use a tool changer with several simple yet specialised tools. This approach enhances reliability and reduces overall costs.
Each new gripper design incurs an engineering cost. Wherever possible, grippers should be designed with reusability in mind to facilitate deployment in similar applications. Modifications such as adjusting the length, changing the type of suction cups or fingers, or adapting the gripper for different robotic arms should be simple and inexpensive. This standardisation minimises design overhead while maximising flexibility.
Rather than attempting to build a perfect gripper every time, treat development as an iterative process. Begin with a simple design and refine it over multiple versions. While straightforward grippers may reach near-perfection within two or three iterations, more complex designs may require ten or more refinements. Continuous improvement leads to optimal performance over time.
A gripper is the most physically exposed part of a robotic system. It comes into controlled contact with objects during every cycle and will eventually wear out or break. Designing the gripper to be easily replaceable by onsite staff and keeping spare units in stock can significantly reduce downtime. With proper planning, a potential outage that could last days can be reduced to just a few.
At one point, we had two types of robots – one dedicated to fashion and one to general merchandise.
The first one utilised a single suction cup connected to a wide pneumatic tube, maximising air flow – very important when picking polybags. The second one utilised multiple tools on a tool changer with three independent pneumatic channels for great versatility but at a cost of lower airflow per cup. To enable the full potential, we decided to unify those two use cases.
It was possible thanks to a simple but powerful tool we call Triflow. It combines all three pneumatic channels into one, connected to a single suction cup. This maximises airflow, enabling us to pick polybags in loose foil, while still allowing seamless integration of this tool with the Tool Changer. With Triflow we were able to unify two specialised robots into a single one.
This alignment delivered an impressive first-pick success rate of 97% at Arvato (fashion) and 99% at Komplett (general merchandise).
An exceptional gripper is crucial for mastering object manipulation, but it cannot perform effectively in isolation. It must be supported by an advanced vision system, a robust control mechanism, and a reliable robotic manipulator. Humans often take their eyes, brains, arms, and hands for granted, but in robotics, every component must be designed, developed, and integrated to create the perfect solution.
At Nomagic, we specialise in precisely this – bringing together vision, intelligence, and automation to develop seamless, efficient robotic solutions.
Get in touch with Nomagic to see how our innovative technology can take your fulfillment processes to the next level.